Optimal Hydronic Control in CRAC Units An Australian Data Centre Case Study
In today’s digital-driven world, ensuring optimal cooling performance in Data Centres is a critical requirement for maintaining uptime and safeguarding sensitive IT equipment.
This case study highlights how IMI’s advanced hydronic control solutions addressed key operational challenges in a large Australian Data Centre, delivering precision, reliability, and efficiency.
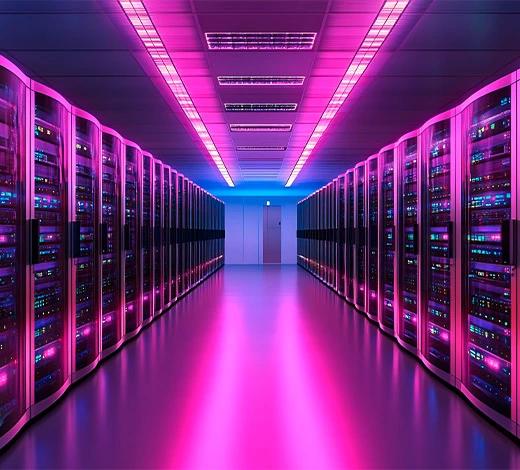
Project Overview
The client, operating an existing chilled water circuit, faced significant operational challenges that impacted system efficiency and performance. The CRAC (Computer Room Air Conditioning) units within the Data Centre required precise temperature and humidity regulation, with each Power Train Unit (PTU) consisting of four CRAC units, totaling 24 PTUs.
The circuit relied on 2-way control valves, isolation valves and differential pressure (Dp) remote sensors for enabling Variable Speed Drive Chiller control on the main chilled water pumps. With this approach, they relied on a plug-and-play commissioning and self-balancing solution provided by the installed CRAC (Computer Room Air Conditioning) units.
Customer Challenges
Stable Differential Pressure Control
CRAC units’ supplier needs to ensure a stable differential pressure for the CRAC unit’s control valve. This valve operates based on gas pressure within the refrigeration circuit and must accurately regulate water flow on the plate heat exchanger (the water-cooled condenser of the CRAC unit). Any fluctuations in differential pressure (Dp) on the water side negatively affected the performance of the control valve, leading to inefficiencies in cooling and increased energy consumption of the CRAC system.
The CRAC unit supplier must ensure a stable differential pressure for the CRAC unit’s control valve. This valve operates based on gas pressure within the refrigeration circuit and is responsible for accurately regulating water flow through the plate heat exchanger (the water-cooled condenser of the CRAC unit). Any fluctuations in differential pressure on the water side can negatively impact the performance of the control valve, resulting in cooling inefficiencies and increased energy consumption of the CRAC system.
Space Constraints
The existing piping network could not be modified, limiting the integration of additional control components. The solution needed to fit within the CRAC unit’s housing while maintaining system performance.
System Efficiency and Reliability
The reliance on plug-and-play commissioning and self-balancing solutions led to inefficiencies, requiring a more precise hydronic control approach
IMI’s tailored Solution
IMI’s technical team proposed two tailored solutions involving the STAP (Differential Pressure Controller) and STAD (Manual Balancing Valve):
- Option 1: STAD + STAP before the 2-way control valve and coil. The STAD valve could be commissioned to meet the full load design flow rate of the CRAC unit. The STAP valve is connected to the STAD valve through a capillary line, to monitor and stabilise the pressure across the condenser heat exchanger. The internal spring of the STAP valve modulates to maintain a stable differential pressure across the condenser heat exchanger and the valve.
- Option 2: STAD + STAP directly across the 2-way control valve. This configuration offered superior control by isolating coil-related pressure variations because the differential pressure of the coil is not part of the STAP’s stabilised differential pressure (Dp), ensuring even greater precision.
Due to space constraints, the client selected Option 1, which ensured stability and efficiency without altering the chilled water system layout.
Results
The implementation of IMI’s solution delivered measurable improvements:
- Enhanced Control Stability: Maintained a constant Dp across the CRAC unit’s control valve, ensuring efficient heat rejection.
- System Efficiency: Optimised cooling performance by stabilising hydronic behaviour.
- Minimal Disruption: Achieved high control performance without requiring modifications to the existing piping network.
Value Delivered
This project underscores the critical role of precision hydronic control in Data Centres, particularly in addressing stability, efficiency, and space constraints.
By implementing IMI’s tailored solution, the client achieved:
- Reliable and consistent cooling performance, reinforcing the critical role of innovative and customisable HVAC technologies;
- Energy efficiency improvements, leading to operational cost savings and supporting 24/7 Data Centre operations;
- A scalable solution adaptable to future Data Centre needs.
IMI continues to lead the way in delivering tailored solutions that align with the unique challenges of Data Centre environments, providing the reliability and performance that today’s digital infrastructure demands.