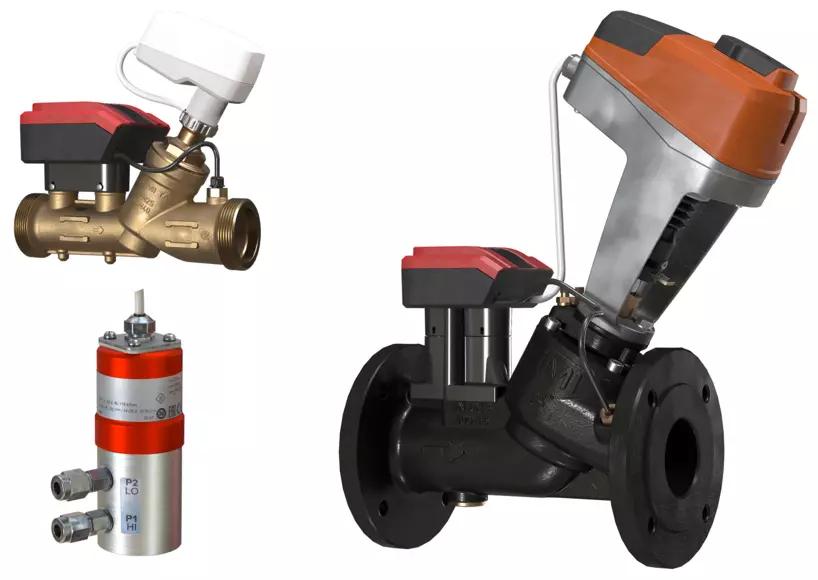
TA-Smart-Dp
Product branding

Features and Benefits
Precise and stable differential pressure control
Delivers desired differential pressure ensuring accurate balancing.
Optional cloud connection
Easy remote access to data and configuration parameters allows to verify and adjust system performance.
High measurement accuracy
High flow and temperature measurement accuracies in all configurations (medium type, and temperature) for all flow regimes.
Compactness and limited number of components
Reduces installation time and space requirements facilitating retrofit installation.
Convenient, reliable setup
Fully customizable and commissionable using Bluetooth enabled smart device reducing commissioning and diagnostic time.
Easy diagnostics
Continuous measurement (flow, temperature, power...) enables accurate error identification in system hydronics.
Versatility in communication
Digital (key Bus protocols and MQTT) and Analog (0(2)-10 VDC or 0(4)-20 mA).
Applications
Heating and cooling systems.
Functions
Reading (flow, power, energy, supply/return temperature, ΔT, position)
Differential pressure control
Measuring (ΔpL)
Pre-setting Δp over the load (ΔpL)
Wireless
Thread
Bluetooth Low Energy (BLE)
Pressure class [PN]
DN 15-50: PN 25
DN 65-125: PN 16, PN 25
Differential pressure (ΔpV)
Flow range
Temperature
Max. working temperature: 110°C
Min. working temperature: -10°C
Operating environment: 0°C – +50°C (5-95%RH, non-condensing)
Storage environment: -20°C – +70°C (5-95%RH, non-condensing)
Dp sensor
Min. working temperature: -15°C
Operating environment: -15°C – +80°C (5-95%RH, non-condensing)
Max. working temperature: 80°C
Storage environment: -40°C – +80°C (5-95%RH, non-condensing)
Media
Water or neutral fluids, water-glycol mixtures (0-57%).
Supply voltage [V]
24 VAC/VDC ±15%. Frequency 50/60 Hz ±3 Hz
Dp sensor
18-33 VDC or 24 VAC +15/-10 % (0-10 V)
Power consumption
Input signal
By BACnet/Modbus
Output signal
0(2)-10 VDC, max. 8 mA, min. 1.25 kΩ.
BACnet/Modbus
Measurement accuracy
Leakage rate
DN 15-50: Leakage rate < 0.01% of q, nom with correct flow direction (Class IV according to EN 60534-4)
DN 65-125: Tight sealing with correct flow direction (Class V according to EN 60534-4)
Pipe connection
DN 15-50: External thread according to ISO 228.
DN 65-125: Flanges according to EN-1092-2, type 21. Face to face length according to EN 558, series 1.
Temperature sensor cable
10 m halogen free cable on request.
DN 15-50: 3 m halogen free
DN 65-125: 5 m halogen free
Material
Surface treatment
DN 15-50: Non treated
DN 65-125: Electrophoretic painting
Ingress protection
IP54 (according to EN 60529)
Protection class
(according to EN 61140)
Certifications and directives
EMC-D. 2014/30/EU: EN 60730-1, -2-14.
Dp sensor: CE certification EN 61326-2-3.
PED: 2014/68/EU
Product standards EN 60730-x.
The table below assists you in finding the relevant product based on its variant. For more details, please download the datasheet above.
Art. No. |
---|